CMMS : What is Computerized Maintenance Management ?
A CMMS (Computerized Maintenance Management System) software allows companies to plan and manage maintenance tasks.
Essential Tool for Maintenance Technicians:
CMMS creates a quality management system for equipment operation and maintenance, aligning with operational excellence strategies.
Our DOMMS CMMS Software:
DOMMS CMMS software is indispensable for addressing safety, productivity, and reliability challenges in your company’s assets.
CMMS Software: Definition and Functionality
CMMS : Definition
A CMMS (Computerized Maintenance Management System) software is a solution used by companies to remotely manage operation and maintenance activities across various sectors. This maintenance management software is particularly recommended for manufacturing industries, energy production, and any businesses or public services that need to maintain infrastructures.
What is the purpose of maintenance management software?
A CMMS (Computerized Maintenance Management System) is essential for optimizing the management of all types of maintenance operations (corrective, preventive, conditional, predictive) within companies. This solution automates and streamlines maintenance processes, providing a precise, real-time overview of operations.
In summary, knowing what to maintain and how before it degrades or fails allows you to :
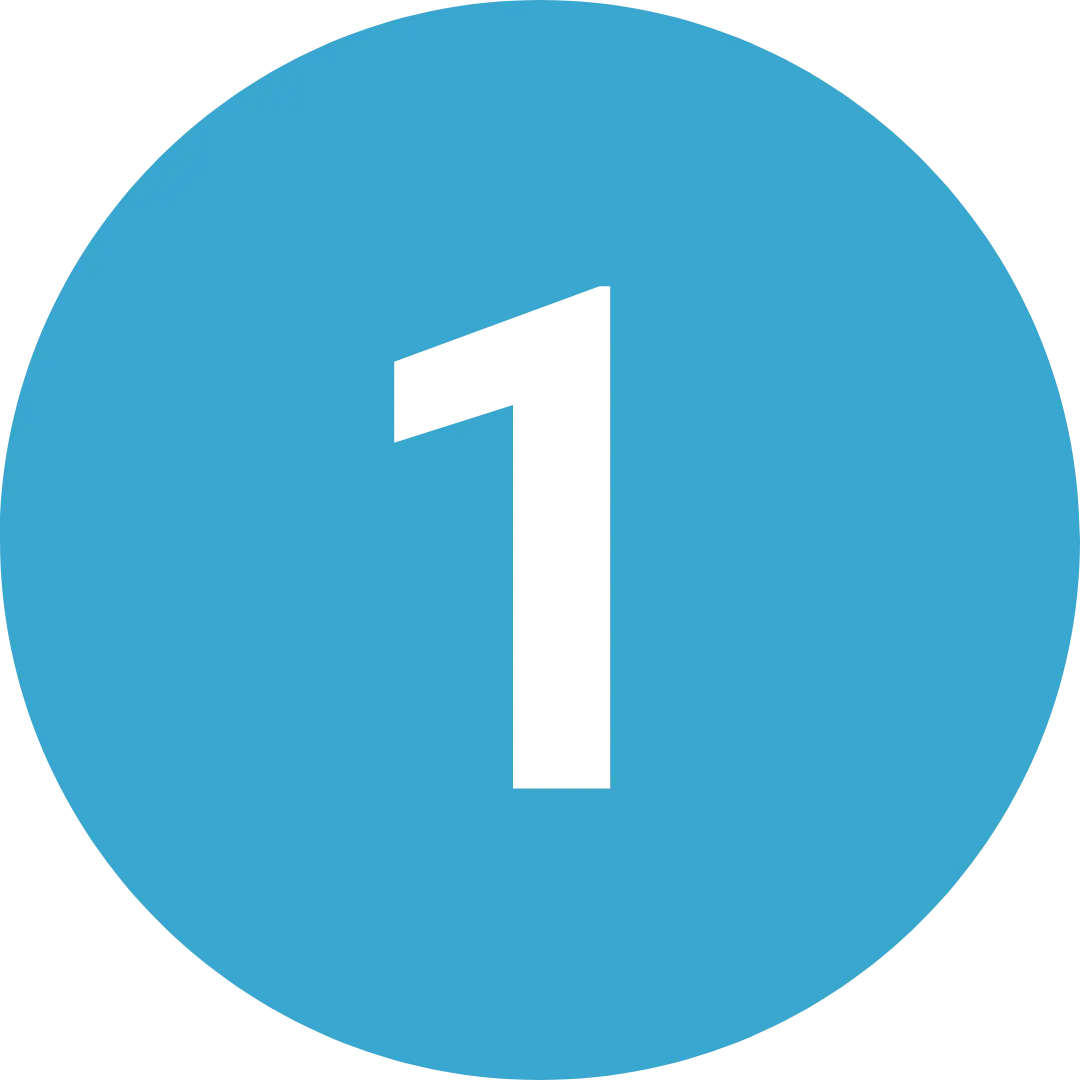
Increase Productivity
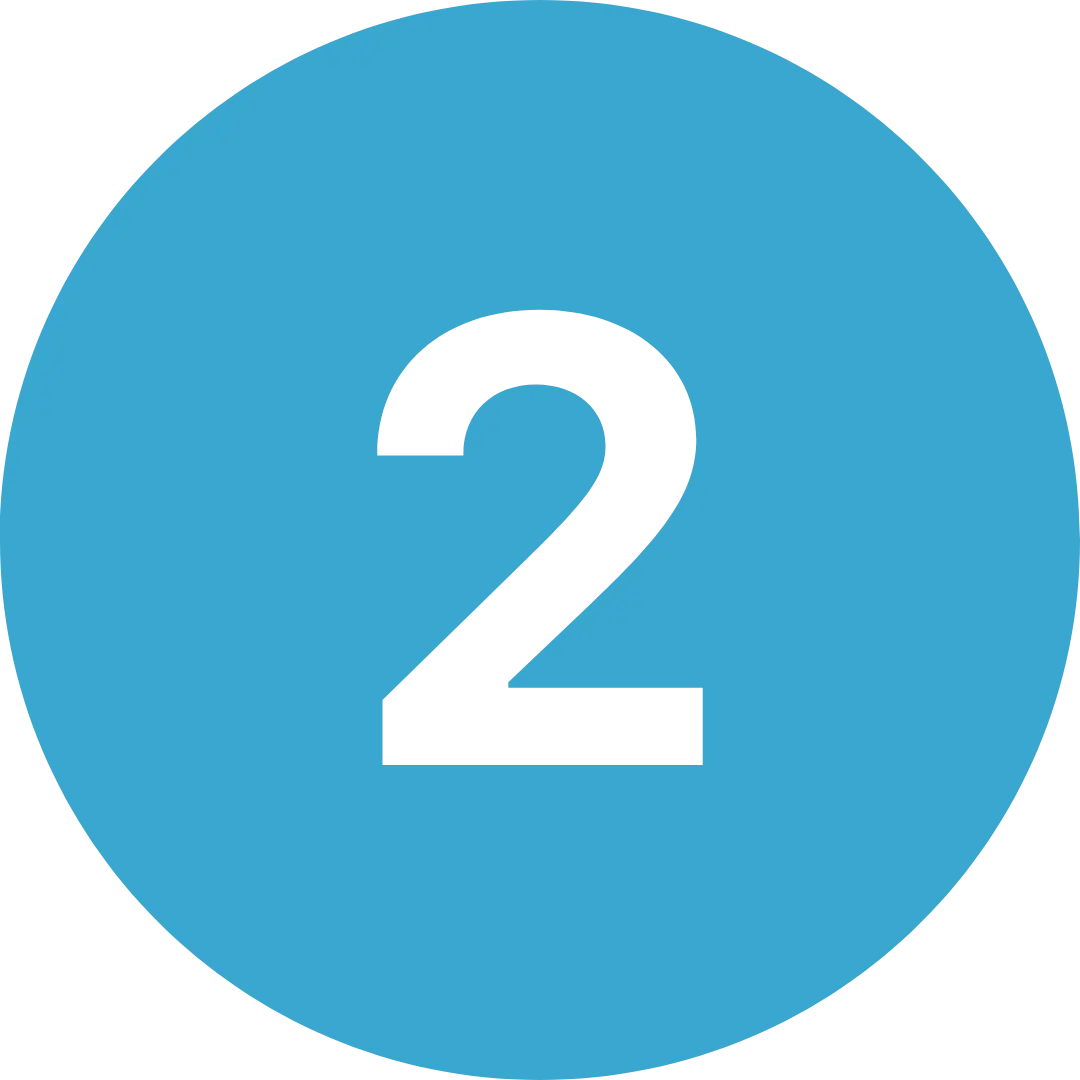
Optimize operational and maintenance costs
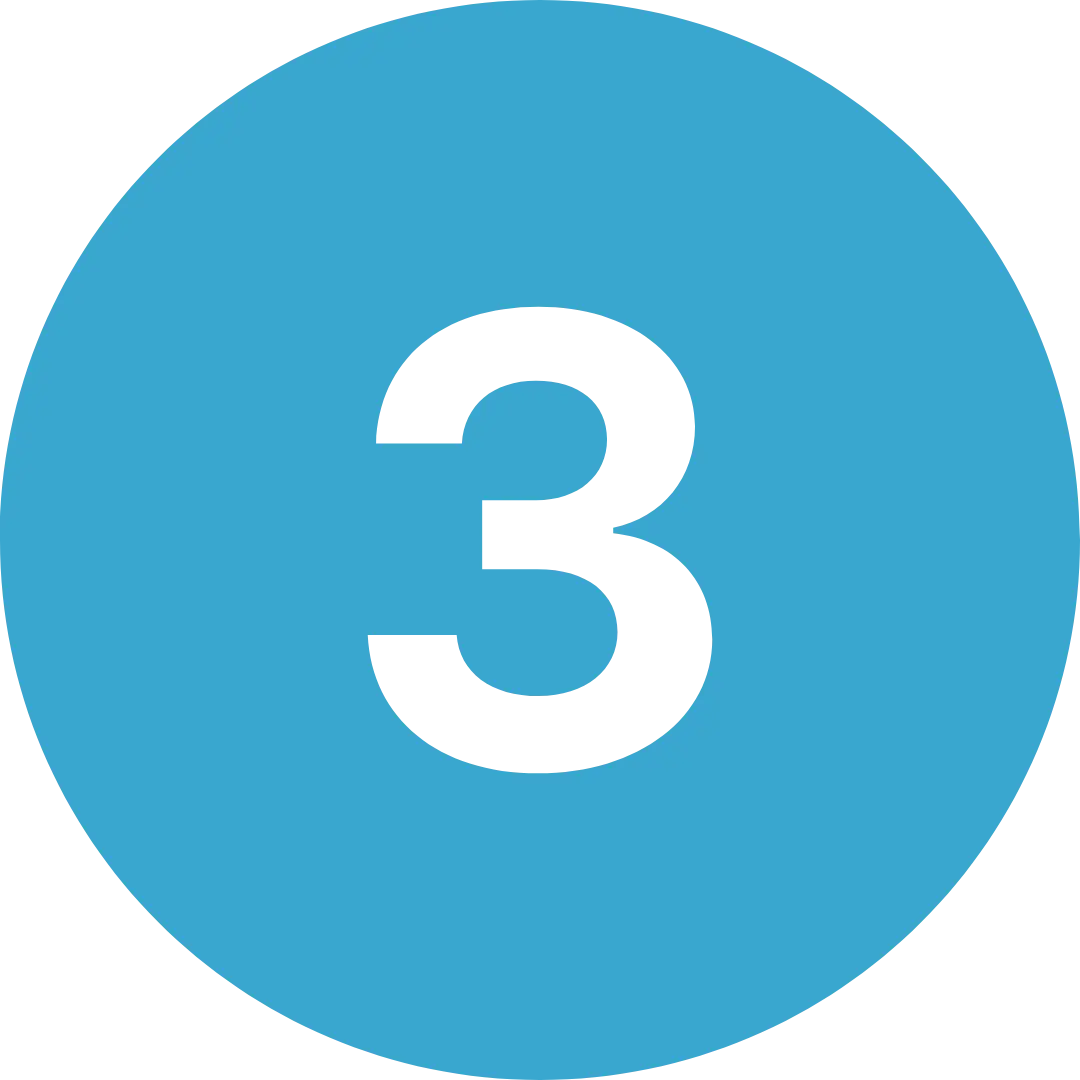
Extend equipment lifespan
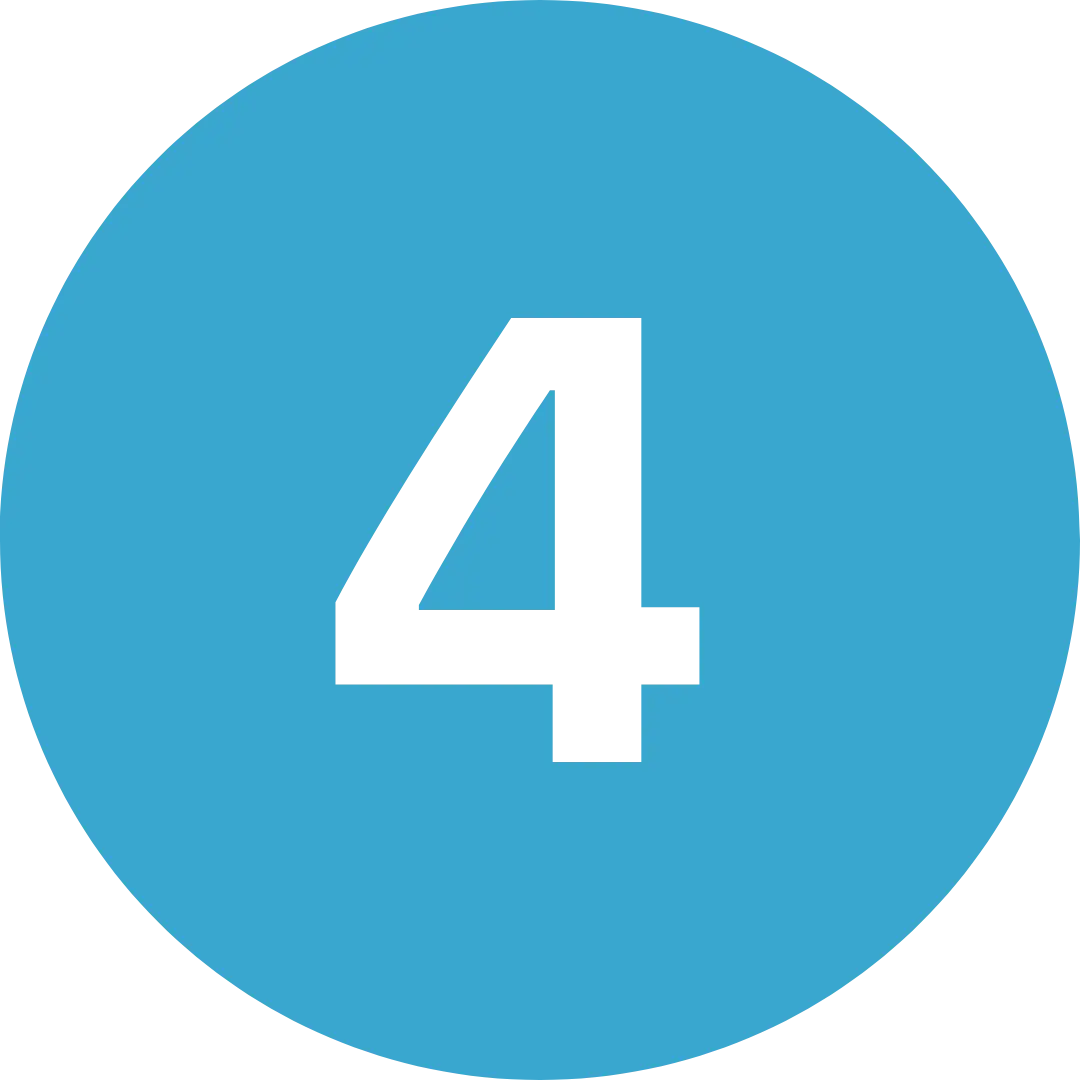
Reduce risks associated with material failures
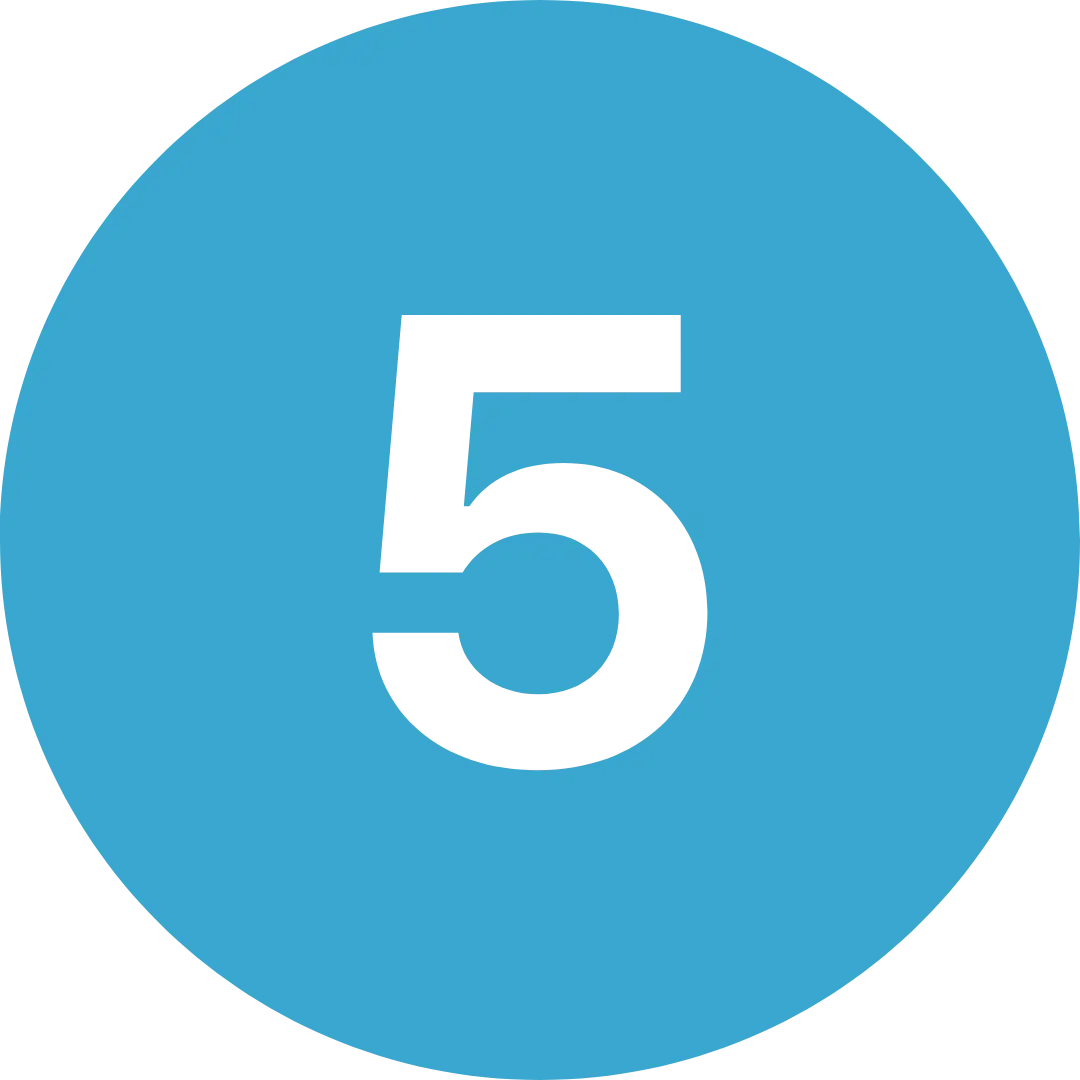
Optimize spare parts inventory management
A maintenance management software aims to reduce failure risks and improve the useful lifespan of equipment.
Computerized Maintenance Management System : All Features
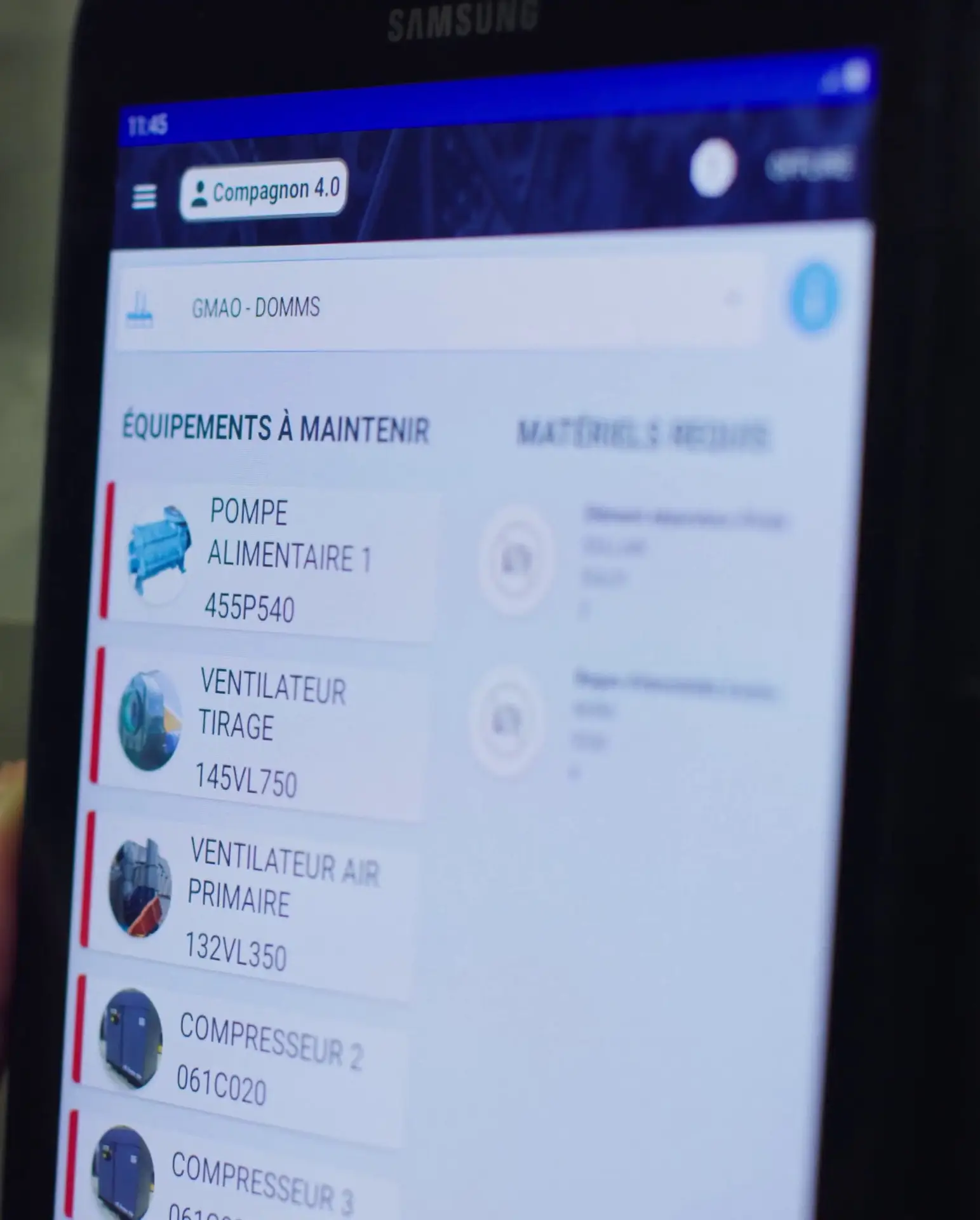
CMMS software is designed to facilitate the planning, tracking, and execution of maintenance tasks. It allows companies to:
- Efficiently manage spare parts inventory, controlling and tracking multi-site equipment.
- Schedule interventions and inspections, handling requests and organizing preventive and corrective maintenance with technician scheduling.
- Track equipment performance through customized KPIs (maintenance completion rate, preventive vs. corrective maintenance ratio, anomaly rates, MTTR, MTBF).
- Manage alerts (anomalies during rounds or intervention requests) and follow up on maintenance actions.
- Provide technical documentation, centralizing all equipment data (visit dates, equipment information, manuals, schematics).
- Ensure compliance with safety standards and regulations.
- Planning & scheduling of maintenance interventions
- Multi-site management.
- Operational dashboard
- Catalog & management of equipment and spare parts
- KPI reports & analyses
- Anomaly tracking
- Electronic Document Management (EDM)
- Mobile application
CMMS : Benefits ?
A key pillar for companies aiming to optimize maintenance operations, CMMS aims to extend equipment lifespan and improve overall performance. By adopting this digital tool, companies enhance resource management, significantly reduce downtime, and increase market competitiveness. Unlike paper documentation, which is prone to wear, loss, or input errors, CMMS software centralizes information, aids decision-making, and shares data efficiently among users.
Improvement of Maintenance Service Performance
- Traceability and Intervention History : Keeps a detailed record of maintenance activities.
- Real-Time Information Access : Provides real-time data and feedback during interventions.
- Preventive Maintenance Optimization : Enhances preventive maintenance efficiency.
✅With a CMMS
Maintenance technicians have constant access to information via tablet or mobile, with or without network connectivity. They can view intervention histories, access technical documentation, and log operations. CMMS ensures the traceability of interventions and their processing.
❎Without a CMMS
Technicians spend time managing intervention reports and accessing documents and procedures, leading to additional costs, information loss, and complexity in consolidating intervention reports and creating comprehensive, relevant reports.
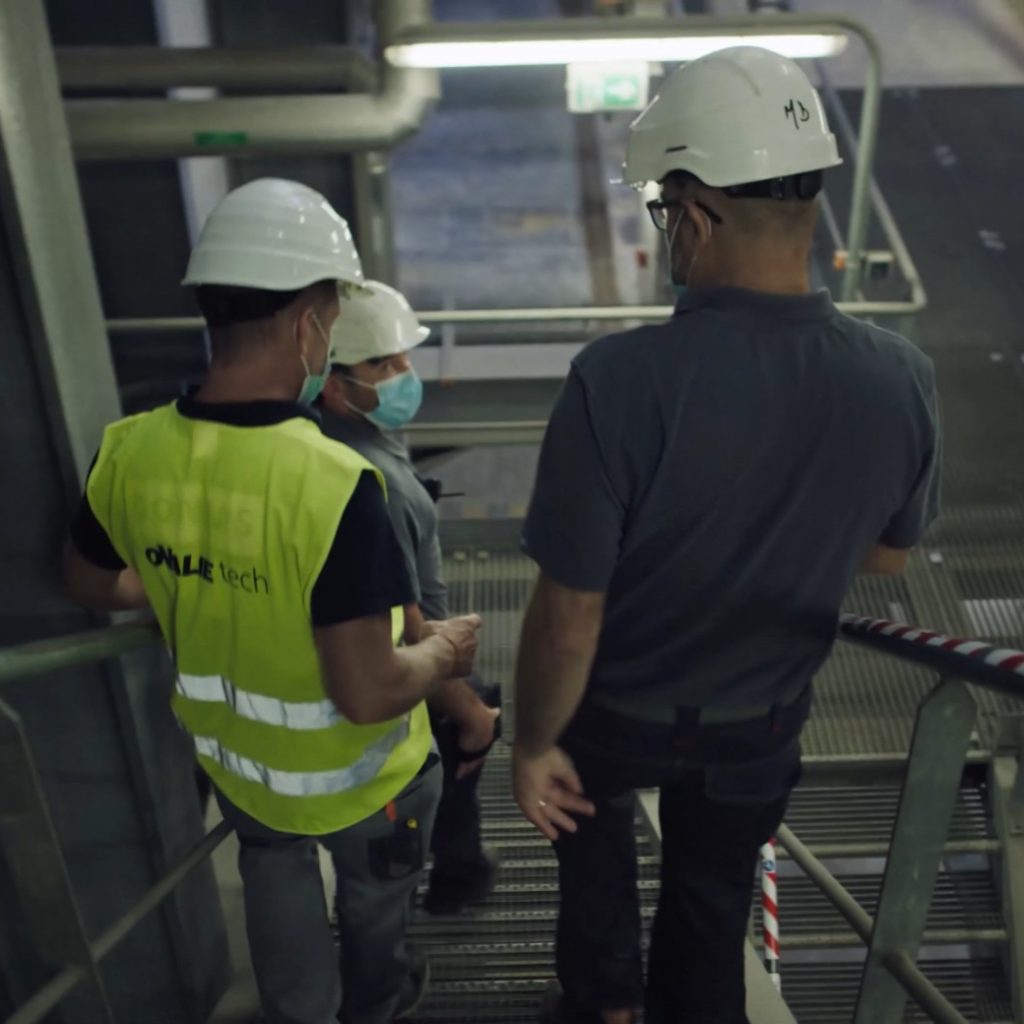
Strategic Decision Making
- Visual Analysis of Key Performance Indicators (KPIs): Provides clear visualizations for better understanding.
- Identification of Maintenance Ratios: Helps pinpoint types of failures and areas for improvement.
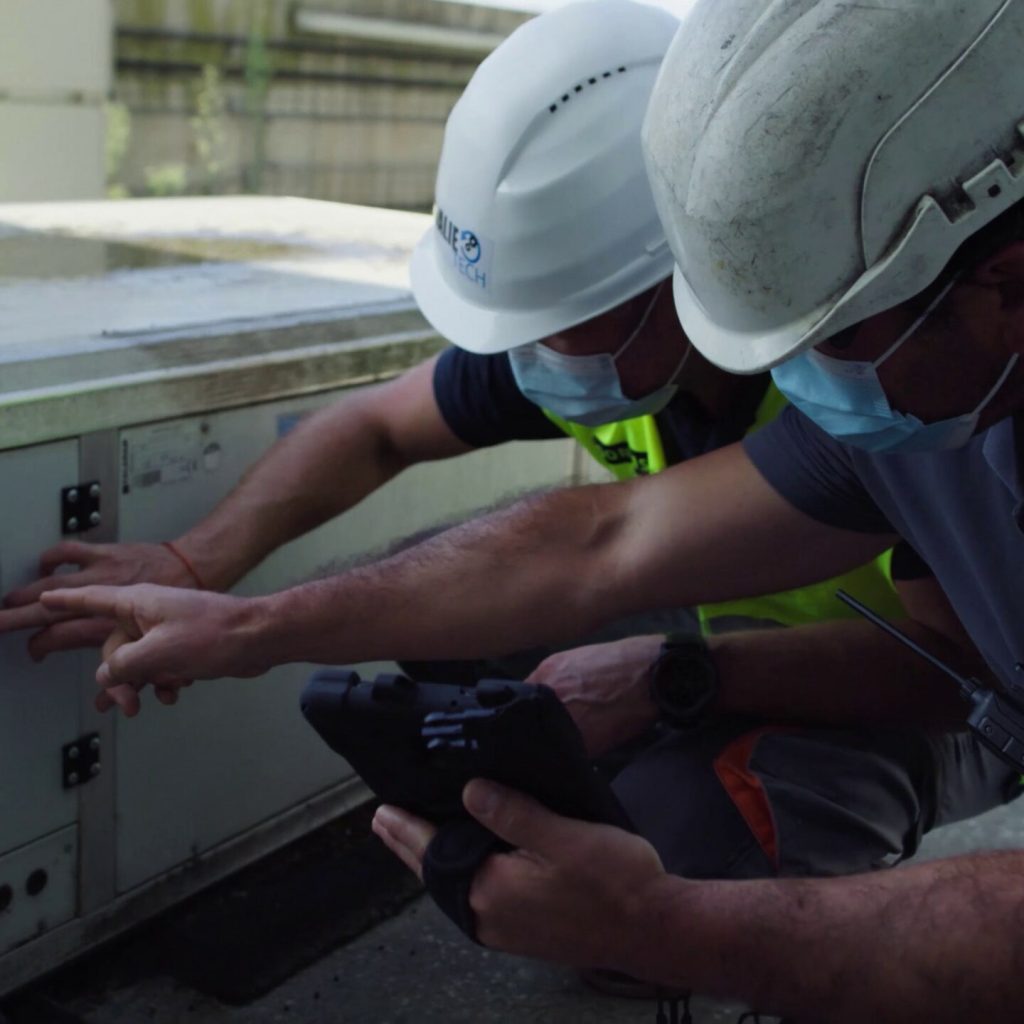
✅With a CMMS
Information is centralized in one place. Coupled with a Business Intelligence tool, CMMS analyzes and visualizes data in dashboards and reports, providing a comprehensive view of activities and aiding decision-making.
❎Without a CMMS
Decision-makers and strategic experts may waste time aggregating data and miss valuable information.
Optimization of Stock Management
- Minimum Threshold Alerts
- Improved Equipment Lifespan and Availability
- Reduced Overstock:
- Financial Management of Stock Value
✅With a CMMS
Spare parts inventories are controlled, references are adjusted to needs, and supplies are planned.
❎Without a CMMS
Risks include:
- Extra costs due to overstocking
- Purchases not matching actual needs
- Lack of necessary spare parts for production
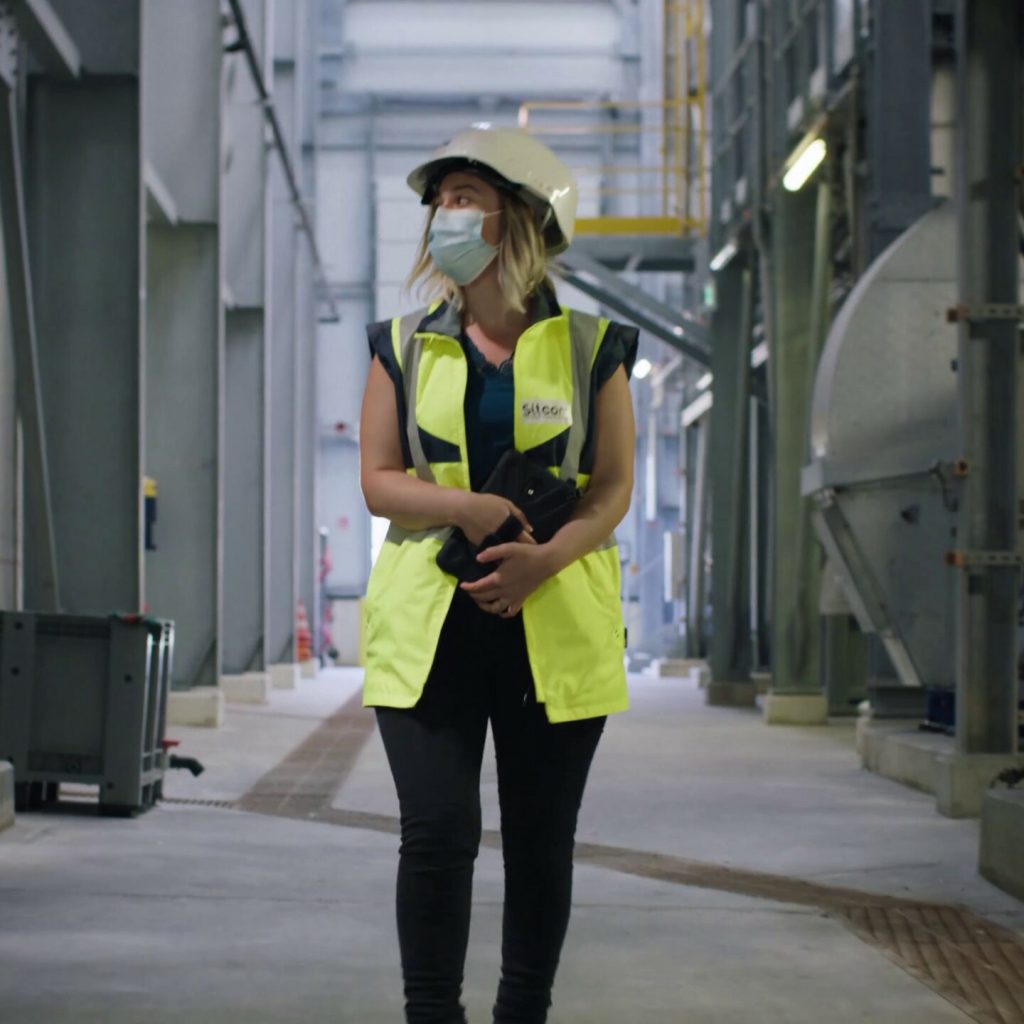
Improving Maintenance Safety
- Reduction in Accidents and Incidents
- Optimized Working Conditions
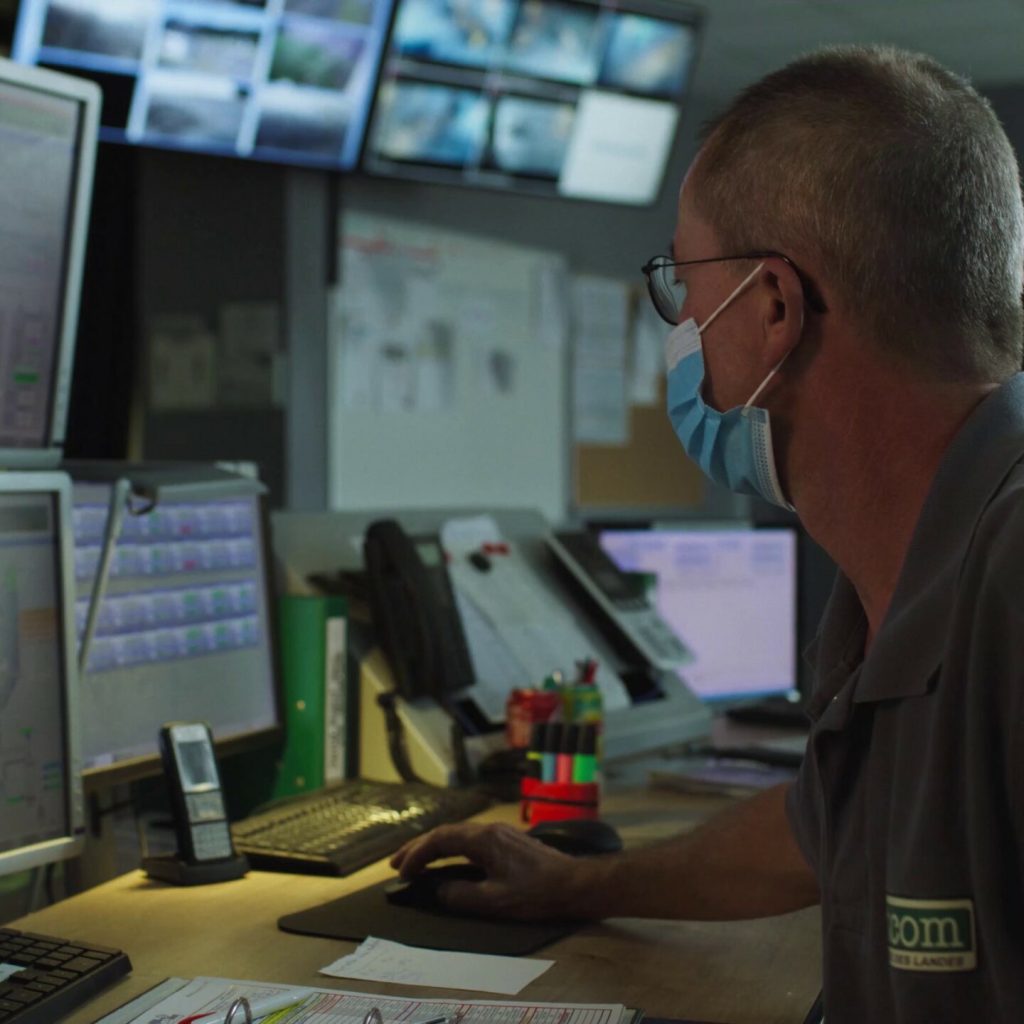
✅With a CMMS
Optimal Safety Conditions: Integrates prevention plans and safety instructions, schedules maintenance, centralizes equipment information, and optimizes communication among technicians.
❎Without a CMMS
Lack of Coordination and Systematic Monitoring: Leads to neglected safety procedures, increasing the risk of accidents or failures.
Strengthening Regulatory Compliance
- Adherence to Safety Procedures
- Regulatory Documentation
- Standards and Regulations Tracking
✅With a CMMS
Mandatory Maintenance Operations: Ensures compliance with regulatory maintenance requirements, meeting deadlines, preparing for inspections, and documenting maintenance activities in regular reports.
❎Without a CMMS
Risk of Non-Compliance: Without a maintenance management system that integrates applicable standards and regulations, there is a risk of failing to perform necessary follow-ups and ensuring their traceability.
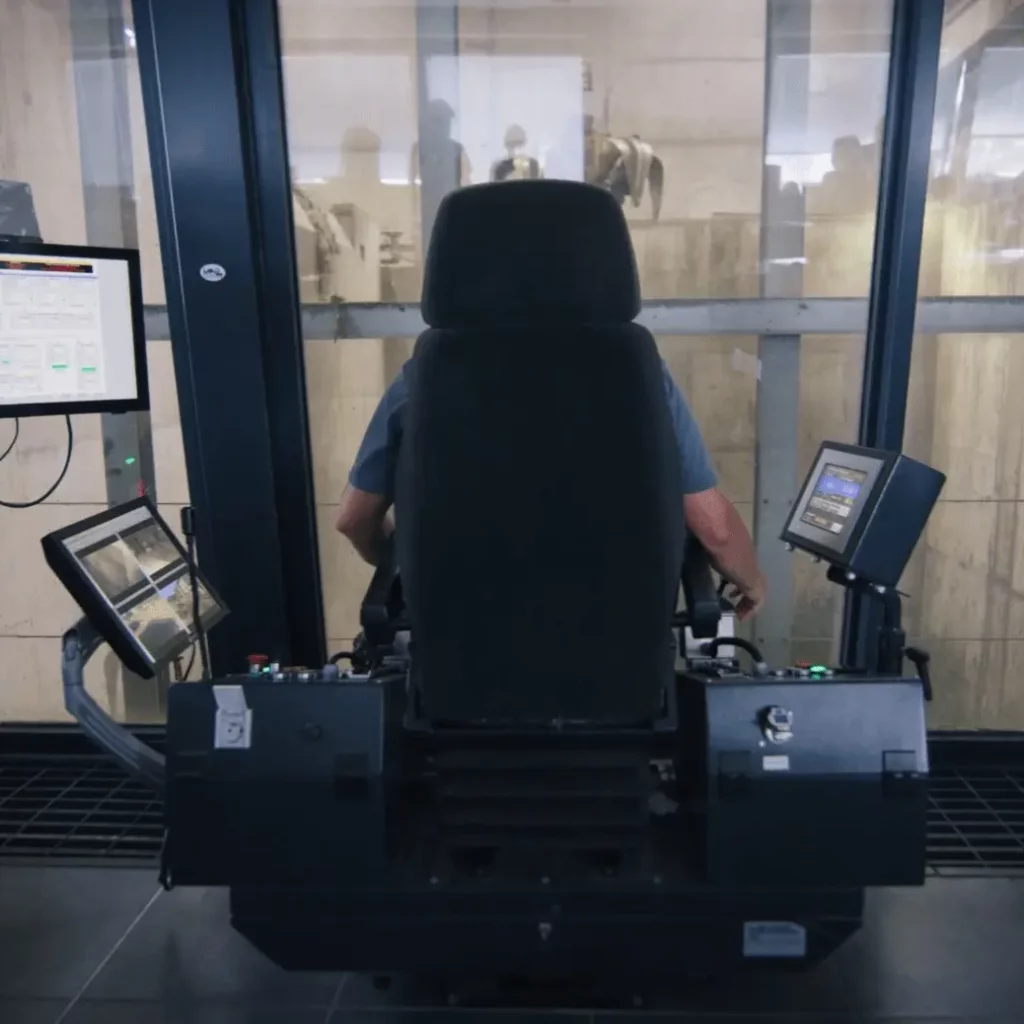
CMMS Software : Sectors and User Types ?
CMMS : sectors
- Industries and Agro-industries: Maintain equipment functionality
- Public Services: Maintain extensive and complex infrastructures
- Buildings and Real Estate Maintenance: Maintain building systems (HVAC, etc.)
- Healthcare Facilities: Ensure medical equipment functionality
- Energy Sector (Methanization, Hydroelectricity, Photovoltaics): Optimize installation maintenance
CMMS : users ?
- Maintenance and operations experts
- Technical services for equipment maintenance
- Operational excellence management
- Purchasing for spare parts and equipment
- Financial analysis of costs and expenses
- IT department for system management
DOMMS CMMS Software : Created by Technicians for Maintenance Technicians
The DOMMS CMMS software offers an ergonomic tool with a 360° view of all maintenance activities. It is designed for industrial asset management, including site operation and maintenance, and features:
- A web interface for control, configuration, and scheduling
- Mobile applications for both online and offline field use
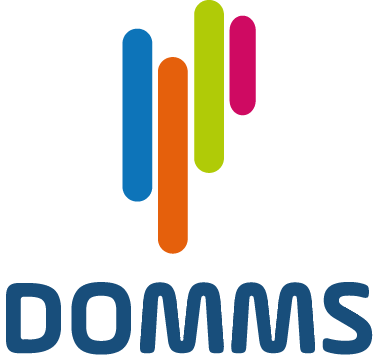
Get a Comprehensive View of Your Industrial Assets
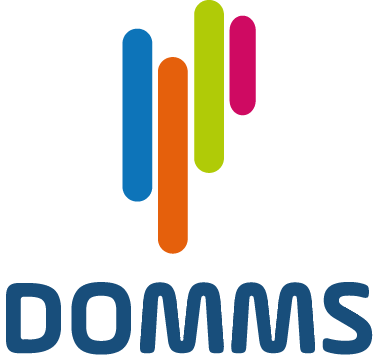
Obtenez une vue d’ensemble sur votre patrimoine industriel.
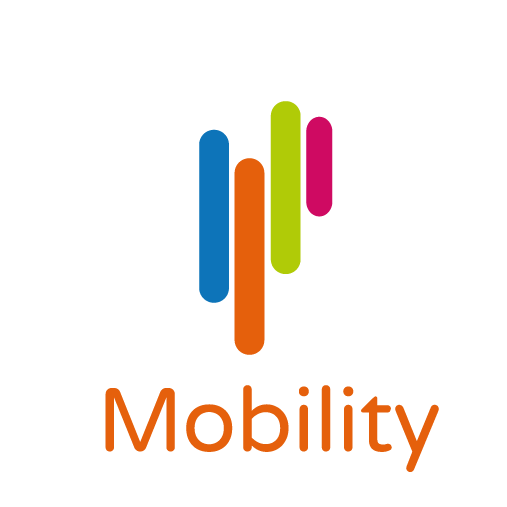
Conduct Your Interventions with Adapted Features
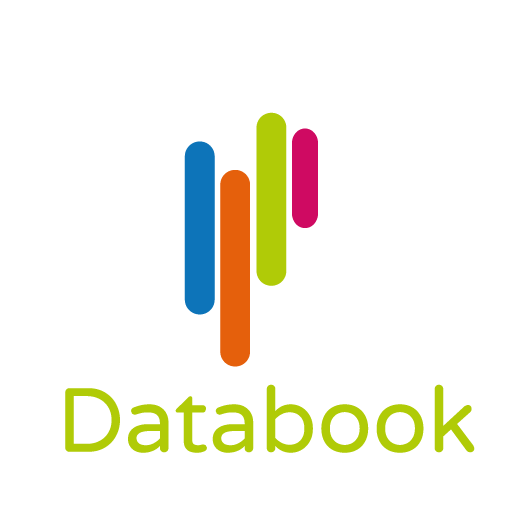
Access All Your Technical Documentation Anywhere
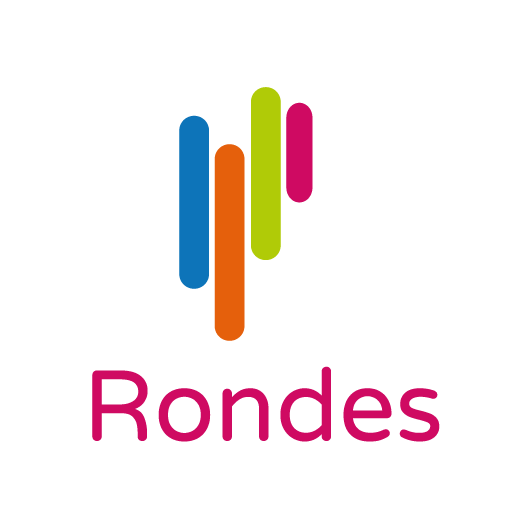
Perform Paperless Rounds
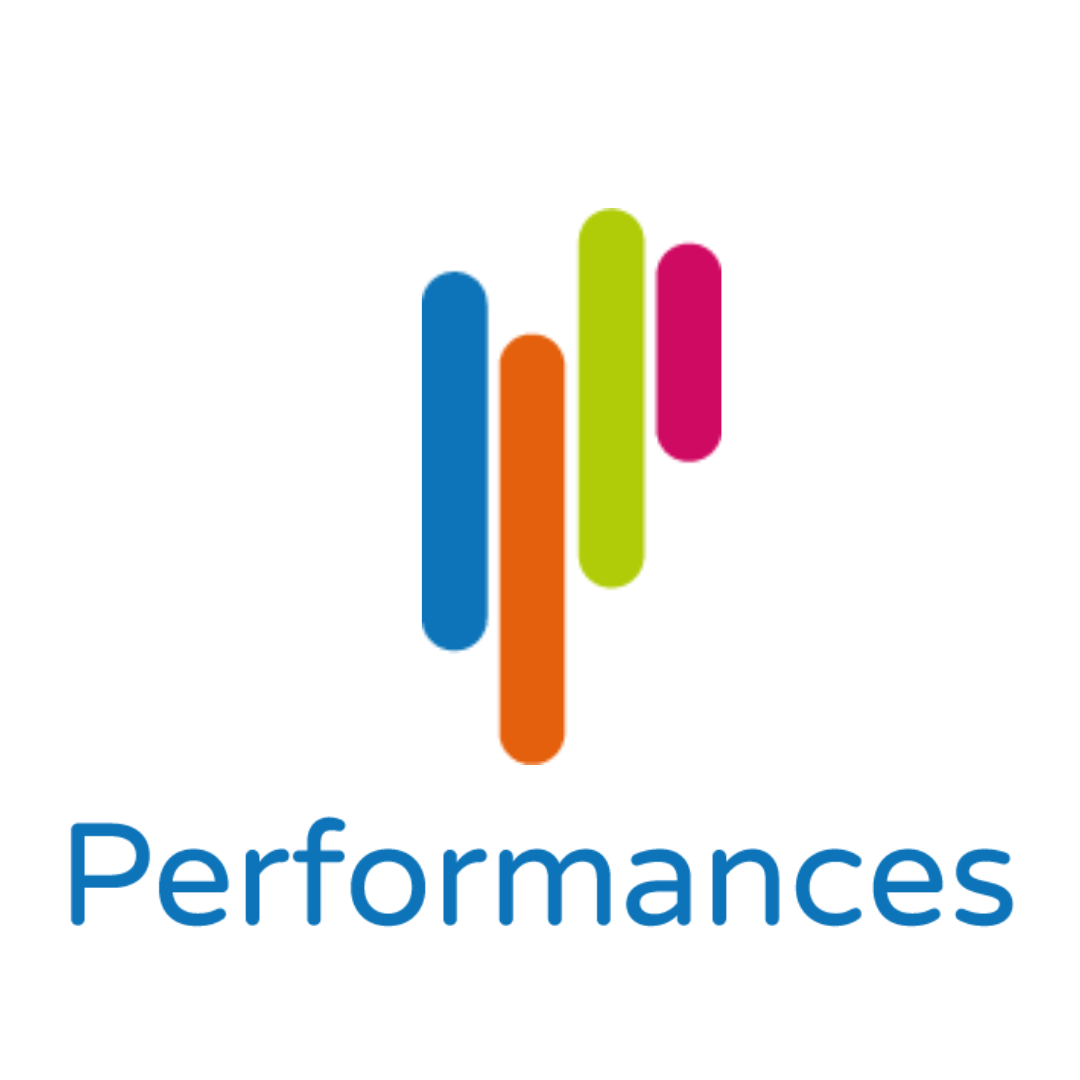
Monitor Your Installations with Dynamic Dashboards
Maintenance and CMMS : A Brief History
In the 1950s, maintenance was primarily simple repairs and upkeep, far from the preventive role it plays today. It evolved to increase production times, meet rising production demands, and reduce downtime during industrial growth. In the 1970s, methodologies like TPM, Kaizen, and 5S highlighted the need for efficiency between production and maintenance, emphasizing preventive maintenance to enhance equipment lifespan and availability.
From the 2000s, Industry 4.0 integrated digital tools, robotics, smart industry practices, data analysis, and AI, revolutionizing maintenance and production through enhanced connectivity.
Between 1980 and 2000, market competitiveness forced industries to boost productivity. As production rates increased, even minor breakdowns became costly, leading companies to rethink maintenance strategies, focusing on preventive maintenance, which evolved into predictive maintenance.
Maintenance encompasses the technical, administrative, and management actions throughout an asset’s lifecycle, aimed at maintaining or restoring it to perform its required function.
The transformation of industrial maintenance coincided with the advent of computing in the 1990s and 2000s, gaining importance across departments (safety, HR, production, finance). Maintenance became digitalized with early CMMS systems, initially limited in functionality and user interface.
With technological advancements, especially through the Cloud, CMMS solutions have become more sophisticated, modular, and user-friendly, accessible from laptops or tablets.